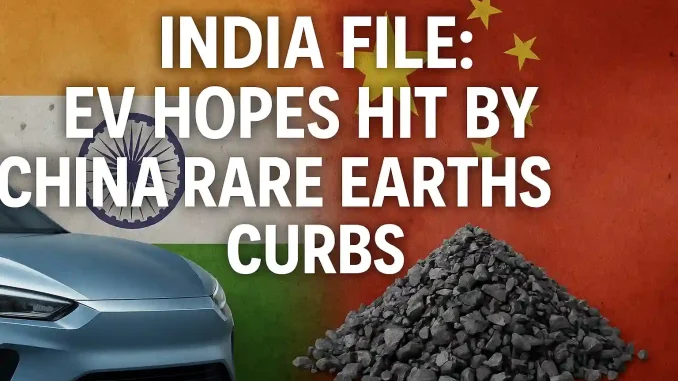
New Delhi – India’s electric vehicle (EV) aspirations have hit a serious roadblock as China tightens its grip on the export of rare earth materials—critical components for the production of EV motors and batteries. The move, aimed ostensibly at boosting domestic security and technological self-reliance, has sparked ripples across global supply chains, and India finds itself particularly vulnerable.
With over 90% of the world’s rare earth processing controlled by China, India’s automotive sector—especially the burgeoning EV market—is grappling with an escalating crisis that could slow down production, raise costs, and derail national electrification targets.
The Rare Earth Dilemma
Rare earth elements like neodymium, praseodymium, and dysprosium are indispensable for making powerful permanent magnets used in EV motors. China, by far the largest producer and refiner of these materials, recently imposed stringent controls on exports, requiring companies to obtain end-user certificates (EUCs) and gain prior government approval for shipments.
This policy shift—quietly rolled out in early 2025—has led to massive delays in shipments to Indian firms. Several auto component manufacturers have reported being in “limbo” as magnet orders await export licenses. Without a timely supply of magnets, motor production has slowed, threatening vehicle assembly timelines and sales rollouts.
“Magnet shipments that used to take four weeks are now taking over 10 weeks,” said an executive at a leading Indian EV component supplier, requesting anonymity due to the sensitivity of the matter. “We’ve had to hold up some of our deliveries to OEMs.”
India’s EV Push at Risk
India has set ambitious goals for EV adoption under the Faster Adoption and Manufacturing of Electric Vehicles (FAME) scheme and the National Electric Mobility Mission Plan. The government targets a 30% share of EVs in new vehicle sales by 2030. Industry giants like Tata Motors, Mahindra Electric, and startups like Ola Electric are pouring investments into EV production facilities and new model rollouts.
However, without a steady supply of rare earth magnets and materials, these plans risk delays and cost escalations.
According to a report by the Society of Indian Automobile Manufacturers (SIAM), India currently imports nearly 85% of its magnet needs from China. A majority of these go into two-wheelers, e-rickshaws, and compact EVs. The sudden clampdown has already led to a ~12% rise in magnet prices in the domestic market.
“We are actively working with the government to find alternative supply chains,” said a spokesperson from Tata Motors. “But shifting dependencies in such a niche and high-tech material space will take time.”
Government in Action: A Multi-Pronged Strategy
The Indian government, recognizing the strategic vulnerability, has sprung into action. According to sources in the Ministry of Commerce and Industry, officials are in “regular contact” with their Chinese counterparts to ensure predictability in rare earth shipments.
In parallel, the government is looking to facilitate imports via end-user certificates (EUCs)—essentially official letters that outline the intended use of imported materials. These EUCs are expected to satisfy Chinese authorities, ensuring that the magnets and rare earths aren’t being diverted to defense or non-civilian use.
Furthermore, New Delhi is also considering a halt on the export of rare earth ores and intermediate products to Japan and other countries, hoping to conserve domestic reserves. “It’s a precautionary move. We are looking to preserve our own rare earth stockpile for domestic use,” a senior official said.
Long-Term Strategy: Self-Reliance in Rare Earths
This crisis has exposed India’s long-standing overdependence on China in critical mineral supply chains. To break this cycle, India is now accelerating exploration of domestic rare earth reserves, especially in Andhra Pradesh, Odisha, and Tamil Nadu. The Indian Rare Earths Limited (IREL), along with other PSUs, is being tasked to scale up mining and processing capacities.
Private players are also being encouraged to enter the rare earth magnet manufacturing space, with incentives possibly being considered under the Production Linked Incentive (PLI) scheme for advanced chemistry cell (ACC) battery storage and components.
India is also in talks with Australia, Vietnam, and the US for long-term strategic partnerships on rare earth supply diversification. Memorandums of understanding (MoUs) have been signed with global miners and refiners to ensure India gets preferential access to non-Chinese sources.
Industry Reaction: Jittery but Hopeful
While the industry is jittery, there is cautious optimism that the disruption might ultimately nudge India toward building more resilient and diversified supply chains.
“This is a wake-up call,” said Ashim Sharma, Partner at Nomura Research Institute. “India has to treat rare earths as a strategic asset, just like oil or semiconductors. This isn’t just an industrial input—it’s an enabler of the green economy.”
Automakers, meanwhile, are considering temporary solutions such as dual-sourcing, designing motors with ferrite-based magnets, or recycling old magnets from e-waste—though these steps come with their own limitations and trade-offs.
Leave a Reply